In recent years, how to continuously reduce the cost per kWh of photovoltaic power generation is the focus of PV business and customers, and is also a necessary path to achieve carbon neutrality. By improving the efficiency of PV cells, the cost of module side can be driven down, thus reducing the investment cost of buyers becomes the main technical path.
However, as cell technology innovation faces a bottleneck, PERC is close to the theoretical efficiency peak, heterojunction, TopCon and other technologies cannot break through the cost barrier in the short term, and the space for each auxiliary material to continue to reduce costs is very limited. How to make PV modules have higher power and power generation, many companies began to do articles on the module "packaging process". This has a high performance and high quality of the module packaging technology in this produced - shingled.
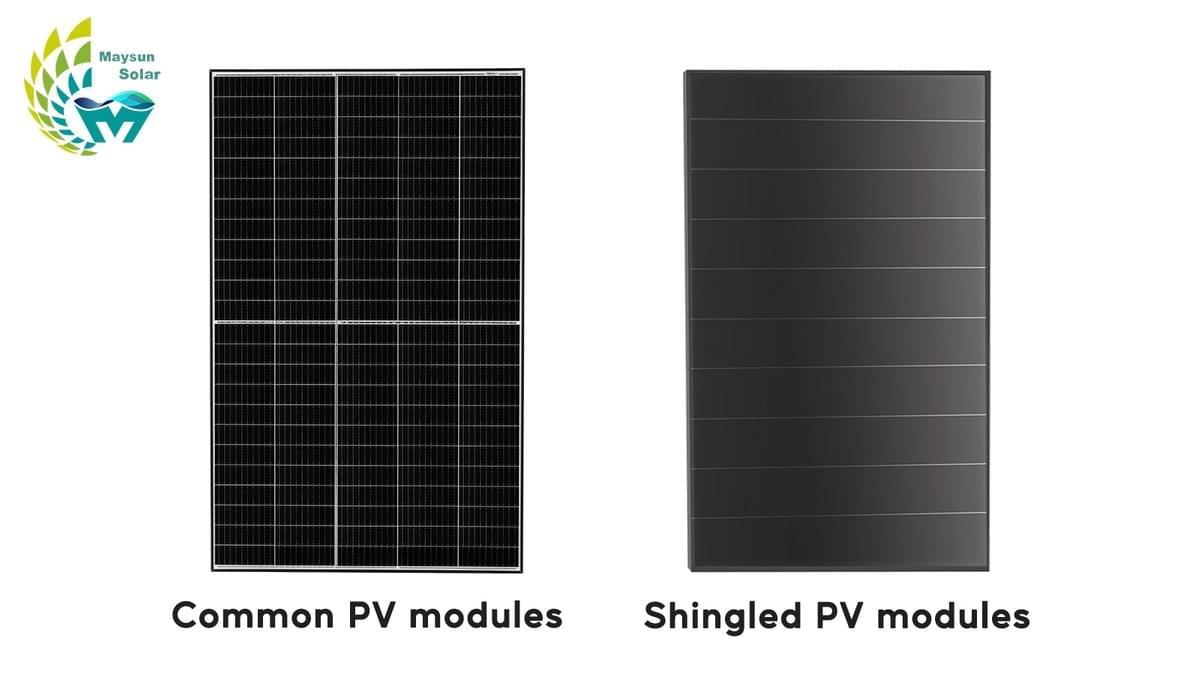
What is shingled technology?
Shingled is the use of laser slicing technology to cut the whole cell into several cell strips, shingled
and arranged in the form of roof tiles, with seamless conductive silver adhesive (ECA) welding technology between the cells instead of metal grid lines, and then laminated packaging. This operation can optimize the module structure, achieve zero cell spacing, and place 5% more cells in the same layout than other types of modules, effectively increasing the module's light receiving area.
The latest generation of high-efficiency shingled technology, which adopts cell surface optimization technology, improves the ability of current collection and can further increase the limit of module packaging energy density. The high-density PV modules encapsulated by shingled technology have five unique product advantages that enable shingled modules to have a stronger "life force" than traditional modules.
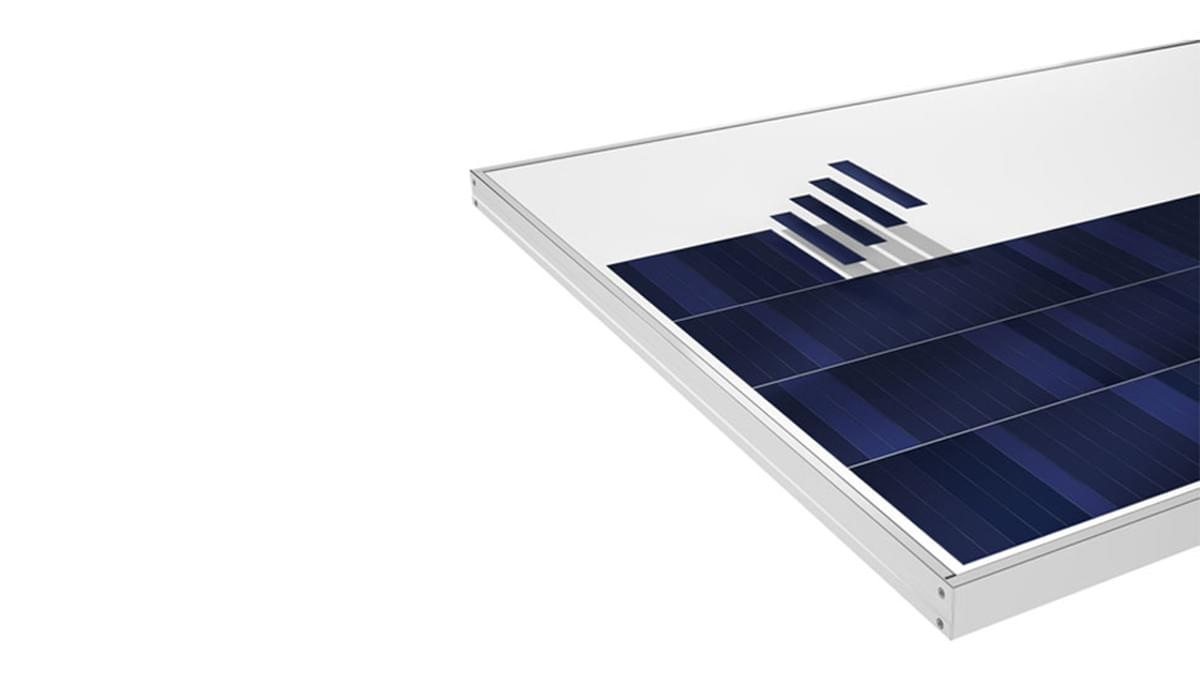
The advantages of shingled technology
1. Higher conversion efficiency
Traditional modules due to the limitations of the welding machine process, generally between the cells have 2mm cell spacing, resulting in many blank area. Shingled module cell and cell stack 0 spacing, in the same area can be packaged more cells, thereby improving the conversion efficiency of photovoltaic modules.
2. Stronger resistance to hot spot
The "hot spot effect" of photovoltaic modules is one of the most important factors affecting the power generation of modules. When the "hot spot effect" reaches a certain level, the continuous local heat will burn the module, resulting in broken glass, scorched cells and burned through backsheet. Even if the module is not burned, the hot spot will directly lead to a 30% shortening of the service life of the PV module, which will cause the PV module to fail in the long run.
Because the working current in the string is 1/6 of the working current in the string of the whole module, the low current can reduce the influence of the reverse current on the hot spot effect of the module, thus greatly improving the anti-hot spot ability of the module.
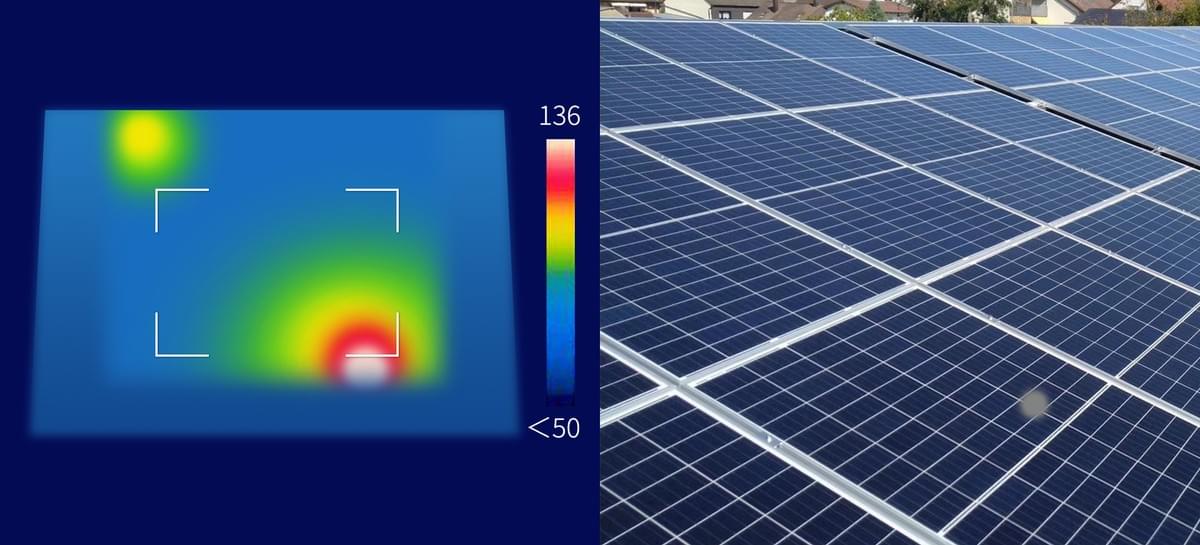
3. Lower risk of hidden cracks
The module with shingled technology, the cells are connected flexibly by ECA, and the stress is evenly distributed, which not only can adapt to thinner silicon wafers, but also make the risk of hidden cracks lower.
When a conventional module is cracked during use, the maximum length of the crack may extend the entire length of the cell (1/2 the length of the half wafer), while the maximum length of the shingled module may extend 1/6 of the entire cell (determined by the number of slices). Shingled modules can effectively limit the effect of occlusion to a smaller area, and even if occlusion occurs, the power loss of the module will be less.
The shading of PV power plant will not only reduce the power generation efficiency of the module, but also may lead to the generation of hot spot, which brings hidden danger to the safety of the power plant. Compared with ordinary PV modules, the impact of shading on shingled modules is much smaller.
When the module is installed vertically, shading the bottom string, the power of the conventional half module decays by 50%, and the power of the conventional whole module decays by 100%. Shingled module only single cell failure power attenuation of 33%; module in the horizontal installation when blocking the bottom of a string, conventional whole, half module power attenuation of 33%, while the shingled module also only single cell failure power attenuation of 17%.
5. Reduce resistance
Finally, in the circuit design, conventional modules use tinned copper tape for interconnection, the resistance of the solder tape is easy to cause power loss. Shingled modules use low resistance ECA for connection, two cells directly connected, the distance between the movement of electrons is shortened, resistance reduction will help to increase power.
Maysun Solar also produces all-black shingled modules in a variety of sizes.
As a PV module manufacturer with 15 years of experience in the industry, Maysun Solar has offices and warehouses in many countries and has established long-term relationships with many excellent installers. Feel free to contact us for the latest module quotes or for PV related questions.
You may also like:
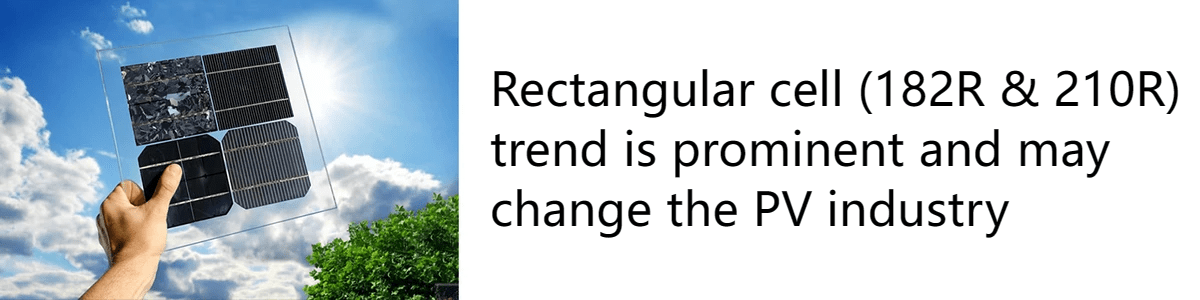
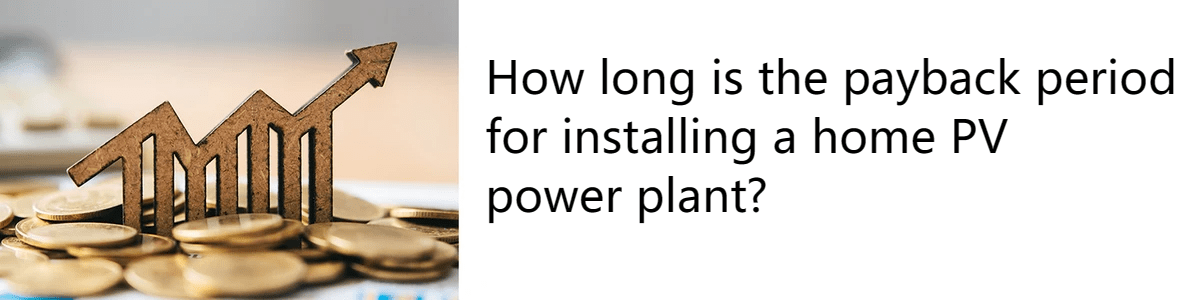