Although a photovoltaic cell already has the ability to generate electricity, but its power generation is too low to use directly, the cells will be connected in series to obtain high voltage, parallel to obtain high current, through a diode (to prevent current back transmission) output, encapsulated in the bezel, installed front glass, back backside, filled with nitrogen, sealed into modules to use. Usually a large PV panel consists of 60 or more cells and has a lifetime of 25-30 years.
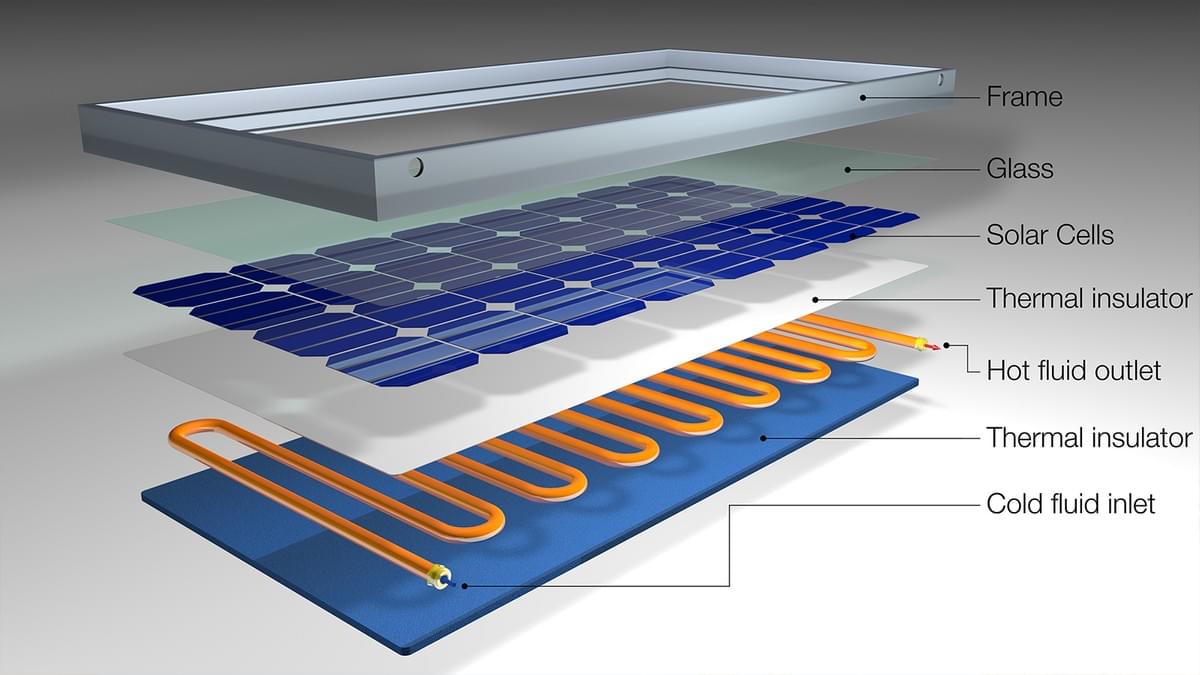
What is the structure of a PV module?
Glass: Most manufacturers use ultra-white calendered glass, which has high solar transmission ratio, low absorption ratio, low reflection ratio, high strength and other characteristics. Subsequent processing, including coating and tempering, can improve the light transmission rate of the glass and increase the strength of the adhesive film (ordinary EVA / white EVA / POE), which is bonded to the glass and backsheet to protect the cells.
Backsheet: It is used to protect the solar cell module against the erosion of the encapsulated adhesive film and cell under outdoor environment, such as light, humidity and heat, and plays the role of weatherproof insulation protection.
Aluminum frame: Combined with organic silicone, it encapsulates and protects cells, glass, backsheet and other raw and auxiliary materials, making the module effectively protected.
Junction box: The electrical energy generated by the solar cell module is exported through the cable.
Other materials: welding tape for the connection between PV module cells, silicone module bezel and backsheet junction box bonding seal, package material module outer packaging materials.
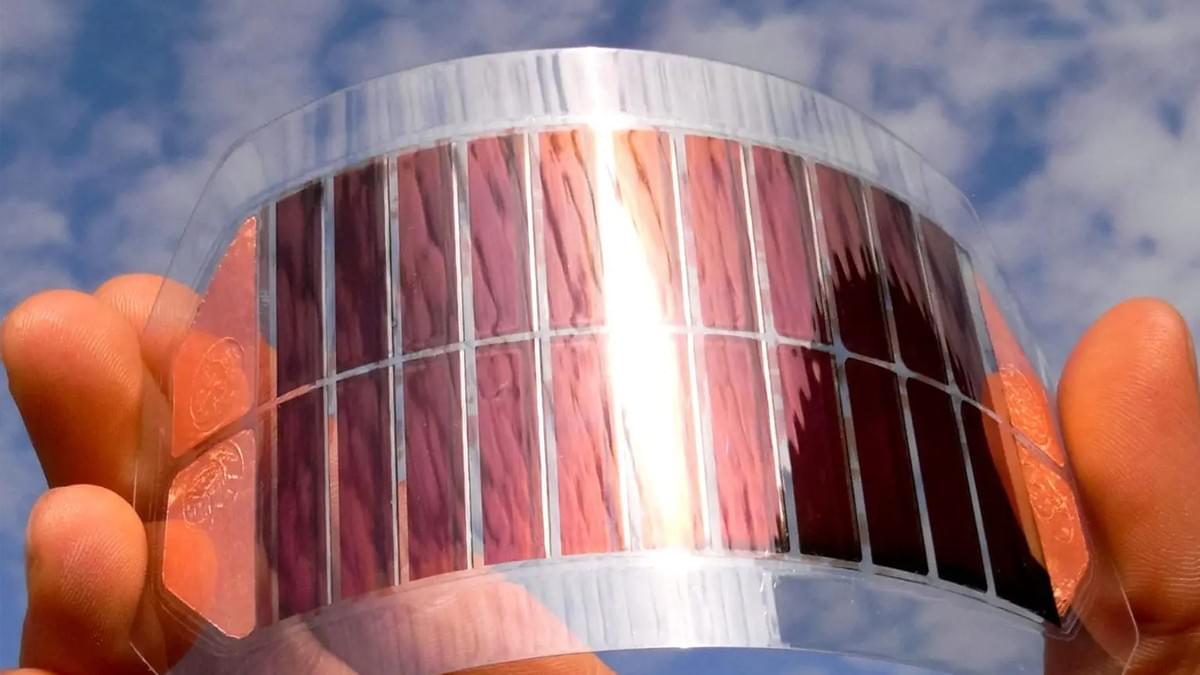
The manufacturing process of photovoltaic modules?
Eight module processes: welding, lamination, laminating, EL testing, frame assembly, junction box assembly, cleaning, IV testing.
1. Welding: Automatic string welding machine will weld the front electrode of solar cell and the back electrode of front and back side cells together through interconnection strips, plate-making machine, automatic welding machine of sink strips will have been welded into a string of cells using sink strips for splicing, the standard number of cells is 60 or 72, corresponding to 10 or 12 copper wires as sink strips to connect them, 6 groups of interconnection for a PV module.
2. Lamination: The backsheet, EVA adhesive, cell group and tempered glass are laminated in order.
3. Lamination: The laminated PV module will be put into the laminator and the air will be extracted from the module by vacuuming, then heating to melt the EVA and pressurizing to make the molten EVA flow to fill the gap between the glass, cell and backsheet film, while discharging the air bubbles in the middle by squeezing, the cell glass and backsheet will be closely bonded together, and finally cooling and curing, the EVA will be melted and extended outward by pressure to form a The rough edges, automatic edge cutting machine to cut the edge.
4. EL luminescence test: Electroluminescent detects internal defects, hidden cracks, fragments, false welding, broken grids and abnormalities of single cell with different conversion efficiencies of solar cell modules. The gap between the frame and the battery component is filled with silicone, and the frames are connected with corner keys.
5. Install junction box: the junction box is glued together with the back plate of the component through silicone, and the lead wires inside the component are connected with the internal lines inside the junction box from the back plate, so that the internal lines are connected with the external cables, and the component is connected with the external cables, and the equipment includes junction box gluing machine and junction box welding machine.
6. Cleaning: Cleaning equipment removes surface dirt, makes the component beautiful, increases the light transmission rate, and increases the component power.
7. IV test: IV test equipment inspects the output power of the module, tests its output characteristics and determines the quality level of the module.
The technical path of PV modules?
In order to improve the output power of a single PV module, the field is constantly researching, and there are currently technologies such as double-sided double-glass technology, stacked tile, HJT, TOPCon, and multi-main grid (MBB). If you want to learn more about the technologies, click on the button to go to the technology page to browse the related professional analysis.
Maysun Solar is a professional PV module manufacturer with 15 years of experience and a systematic and complete PV module production line factory. We welcome you to click for more information!

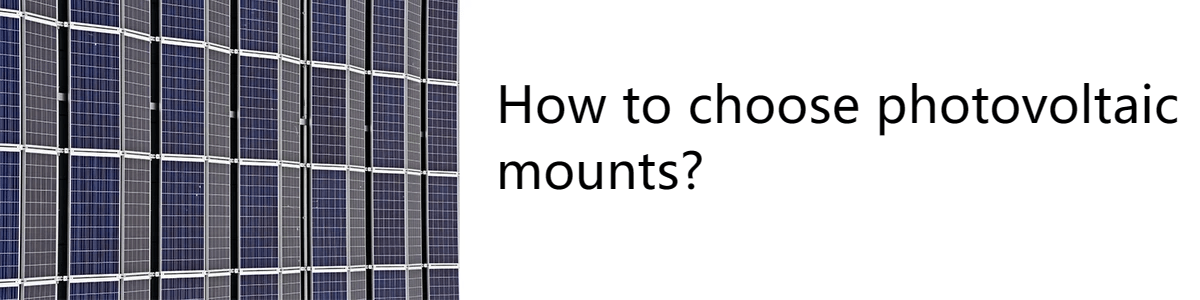