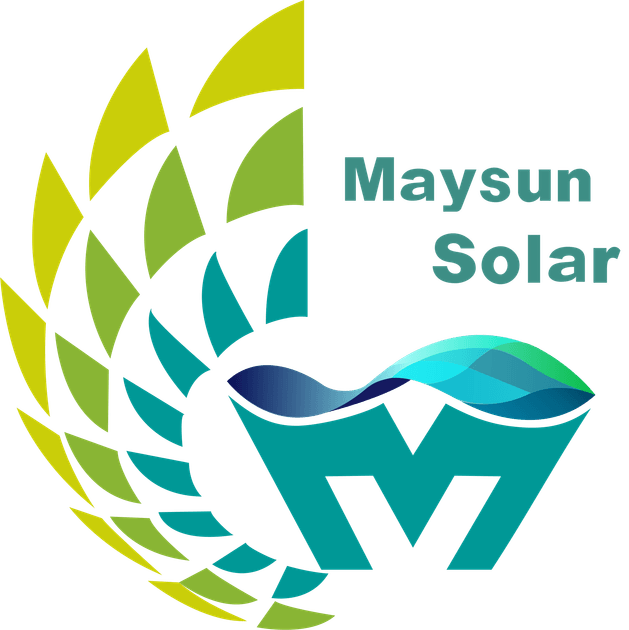
Maysun Solar
- …
Maysun Solar
- …
What is HJT technology for solar modules?
What is HJT Technology?
- HJT solar cells feature a unique double-sided structure, capable of absorbing both direct and scattered light from each side. Utilizing Plasma-Enhanced Chemical Vapor Deposition (PECVD), a remarkably thin layer of intrinsic silicon is used for passivation, along with a P-type silicon doping on the top side of the monocrystalline silicon wafer N, post texturing and surface cleansing. Subsequently, a comparable layer and an N-type silicon doping are applied to the reverse side.
- Following this, we employ PVD magnetron sputtering to deposit a transparent oxide conductive film (TCO) and metal layers on both surfaces of the cells.
- The process culminates with the creation of metal grids on each side, leveraging our state-of-the-art metallization technology.
Structure of HJT Solar Cells
The HJT cell structure, standing for Heterojunction with Intrinsic Thin Layer, also known as HIT, is a symmetrical double-sided cell structure. At its core lies N-type crystalline silicon. Sequentially deposited on the front side are an intrinsic amorphous silicon thin film and a P-type amorphous silicon thin film, together forming a P-N junction. Conversely, the back side of the silicon wafer is layered with an intrinsic amorphous silicon thin film and an N-type amorphous silicon thin film, creating a back surface field. Due to the poor conductivity of amorphous silicon, Transparent Conductive Oxides (TCO) are deposited on both sides of the cell for conduction. Finally, the double-sided electrodes are formed using screen printing technology.
Materials and Components of HJT Solar Cells
Three key materials used in heterojunction solar cells are crystalline silicon (c-Si), amorphous silicon (a-Si), and Indium Tin Oxide (ITO).
Crystalline Silicon (c-Si)
Crystalline silicon (c-Si) forms the backbone of the rapidly evolving photovoltaic (PV) industry, commonly used in the form of crystalline wafers to manufacture standard homojunction solar cells. There are two types of c-Si: polycrystalline and monocrystalline, but only monocrystalline silicon is considered for HJT solar cells due to its higher purity and, consequently, higher efficiency.
Amorphous Silicon (a-Si)
Indium Tin Oxide (ITO) is the preferred material for the Transparent Conductive Oxide (TCO) layer in heterojunction solar cells. The deposition technology of Transparent Conductive Oxide (TCO) films is crucial for the high performance of optoelectronic devices. ITO’s reflectivity and conductivity characteristics make it an excellent contact layer and outer layer for HJT solar cells.
Indium Tin Oxide (ITO)
In the 1970s, it was discovered that amorphous silicon (a-Si) was suitable for thin-film photovoltaic technology and could serve as a semiconductor in solar cells, making it the second most important material in the manufacture of heterojunction solar cells. Although a-Si itself has density defects, hydrogenation processes can address these issues, resulting in hydrogenated amorphous silicon (a-Si:H). This process, which allows for easier doping and a wider bandgap, makes it more suitable for HJT cell manufacturing.
HJT Cell Manufacturing Process
The manufacturing process for HJT cells is relatively short. It mainly consists of four stages: texturing, amorphous silicon deposition, TCO (Transparent Conductive Oxide) deposition, and screen printing. This is significantly fewer steps compared to PERC (10 steps) and TOPCON (12-13 steps). The deposition of amorphous silicon primarily uses the PECVD (Plasma-Enhanced Chemical Vapor Deposition) method. Currently, there are two methods for TCO film deposition: Reactive Plasma Deposition (RPD) and Physical Vapor Deposition (PVD).
How Do HJT Solar Cells Work?
The working principle of heterojunction solar cells is similar to other photovoltaic components. Under the photovoltaic effect, the main distinction of this technology lies in the use of a triple-layer absorbent material combining thin-film and traditional photovoltaic technologies. This process involves connecting a load to the module's terminals, where photons are converted into electrical energy, generating a current that flows through the load.
To generate electricity, photons strike the P-N junction absorber and excite electrons, causing them to move to the conduction band, thereby creating electron-hole pairs (e-h).
The excited electrons are collected by the terminals connected to the P-doped layer, generating a current that flows through the load.
After flowing through the load, electrons return to the cell's rear contact point and recombine with holes, completing that particular e-h pair. As the module generates electricity, this cycle continually occurs.
A phenomenon known as surface recombination occurs in standard c-Si photovoltaic components, limiting their efficiency. In this process, excited electrons pair with holes on the material's surface, causing them to recombine, and the electrons are not collected to flow as current.
To reduce surface recombination, heterojunction cells use a passivating semiconductor thin film to separate the highly recombining active (Ohmic) contacts from the wafer-based layers, featuring a buffer layer made of a wider bandgap layer of a-Si:H. This buffer layer allows the charge flow to be slow enough to generate high voltage but fast enough to avoid recombination before the electrons are collected, thus enhancing the efficiency of heterojunction cells.
In the light absorption process, all three semiconductor layers absorb photons and convert them into electrical energy.
The first arriving photons are absorbed by the outer a-Si:H layer, converting them into electrical energy. However, most photons are converted by the c-Si layer, which has the highest solar energy conversion efficiency among the materials in the cell. The remaining photons are eventually converted by the a-Si:H layer at the back of the module. This three-step process is why single-sided heterojunction solar cells achieve efficiencies of up to 26.7%.
Advantages of Heterojunction(HJT) Technology
- High Efficiency: Features high-efficiency heterojunction (HJT) solar cells and advanced half-cell technology, achieving module efficiencies above 22.87%.
- Large-Sized Cells: Utilizes efficient HJT 210mm solar cells, offering a larger surface area for increased sunlight absorption and higher energy output in a compact form.
- Low Degradation: HJT cells avoid LID, LeTID, and PID effects due to a non-polarizing TCO film, resulting in less than 11.1% power degradation over 30 years, ensuring long-term stable energy output.
- Fewer Processes: The manufacturing process is shorter, mainly involving four steps: texturing, amorphous silicon deposition, TCO deposition, and screen printing; significantly fewer than PERC (10 steps) and TOPCON (12-13 steps).
- Thin-Film Technology: High-efficiency silicon heterojunction (HJT) combines crystalline silicon and amorphous silicon thin-film technologies, offering exceptional light absorption and passivation capabilities.
- Stable Performance in High Temperatures: Exhibits the most stable power temperature coefficient of -0.24%/°C, ensuring stable energy production in high-temperature environments with minimal power loss and consistent yield improvement.
Additional Power Gain: HJT cells with symmetric front and back structures and grid design achieve a back-side utilization rate over 95%, offering more than 30% additional power gain compared to PERC and TOPCON.
Superior Low-Light Performance: By inserting an intrinsic thin-film i-a-Si:H between crystalline and doped thin-film silicon, HJT cells effectively passivate surface defects of crystalline silicon, resulting in higher open-circuit voltage, broader light absorption spectrum, and faster startup in low-light conditions.
Low-Temperature Process: HJT cells use a silicon-based thin-film to form the pn-junction, with soldering process temperatures below 250°C, reducing thermal stress and high-temperature damage to the cells.
No Cell Cutting: The complete half-cell manufacturing process without cell cutting minimizes micro-crack impacts.
High Flexibility: The unique cell structure of HJT cells greatly enhances cell flexibility, reducing the risk of microcracks during transportation and installation, and improving the reliability of power stations.
Comparison ofHJT, TOPCon, and PERC Technology
Heterojunction (HJT) solar panels have high bifacial yield and low temperature coefficients, enhancing power generation efficiency and output, effectively reducing electricity cost. They are particularly suitable for areas in Europe with higher summer temperatures and are ideal for agricultural photovoltaics, solar carports, and photovoltaic fences.
Future Forecast for HJT Solar Cells
Given the multiple advantages of the heterojunction (HJT) solution, it is likely that more companies will continue to adopt this technology in the near future. As the HJT manufacturing process involves four fewer steps than PERC technology, it has the potential to significantly save costs. While PERC has been the popular choice in the industry for many years, its complex manufacturing process cannot compete with HJT. Moreover, PERC does not have the high-temperature performance advantage of HJT.
According to the ITRPV 2019 report, heterojunction (HJT) cells are expected to gain 12% market share by 2026 and 15% by 2029.
Reference:
https://www.kanekaenergysolutions.com/what-is-heterojunction-technology-hjt-in-the-solar-industry
https://solarmagazine.com/solar-panels/heterojunction-solar-panels/#Looking_into_the_future_of_heterojunction_technology
HJT Solar Panels from Maysun Solar
Related Articles About HJT Technology
Copyright © 2011 - 2024 Maysun Solar. All rights reserved.